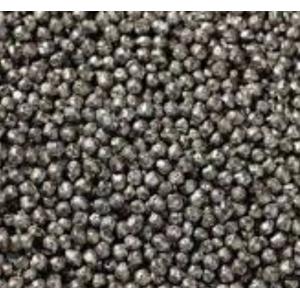
Add to Cart
Cutting Process Mild Steel Shot 0.2mm-3.0mm With Optimal Performance
Forged Grinding Pellets: Grinding pellets, also known as high manganese steel pellets, are forged products. They are created by cutting high-manganese steel wire at high speed into cylindrical shapes, which are then rounded with lead angles. These pellets are characterized by their absence of voids, cracks, and breakage.
Consistent Shape and Size: Grinding pellets undergo a gradual reduction in size during their service life cycle. Starting from larger particles, they progressively become smaller until reaching a size as small as 3/10 of the original particles. At this point, they are removed by the dust extraction system or separation equipment of the shot blasting machine. This complete life cycle ensures optimal usage of the pellets.
Unique Manufacturing Process: Grinding shot represents a new type of steel wire shot. It involves cutting the steel wire into cylinders with uniform length and diameter, followed by grinding to remove edges and corners, resulting in spherical ball-shaped bodies. This innovative manufacturing process combines the advantages of both cast steel shot and steel wire cut shot.
Enhanced Performance and Longevity: The spherical shape of grinding steel shot allows for even polishing without causing damage to the workpiece. Additionally, it exhibits high wear resistance, making it durable and long-lasting even after repeated polishing. These characteristics make grinding steel shot the preferred metal abrasive material for finishing automobile and motorcycle accessories.
a. Unparalleled Impact Resistance and Stability: The bainite structure formed through isothermal transformation gives low carbon steel shot exceptional impact resistance, ensuring stable performance even in the most demanding conditions. This superior resilience sets it apart from other steel shot variants.
b. Exemplary Quality Composition: Low carbon steel shot is meticulously crafted using high-quality, low-carbon, low-residue, low-phosphorus, and low-sulfur new scrap steel. Unlike other types of steel shot, it does not undergo heat treatment, preserving its desired hardness and quality throughout its lifespan.
c. Enhanced Toughness and Extended Service Life: The unique organizational structure of low carbon steel shot contributes to its remarkable toughness, making it highly resistant to breakage. This outstanding durability allows it to withstand approximately 3,600 repeated cycles, significantly reducing consumption by over 20% compared to high carbon steel shot of similar quality.
d. Maintenance and Efficiency Advantages: The round shape of low carbon steel shot ensures smooth contact between the equipment and steel plates, minimizing wear on the shot blasting head and lining. In contrast, high carbon steel shot is prone to breakage, resulting in angular steel shots that increase wear and decrease the efficiency of shot blasting machines. By utilizing low carbon steel shot, businesses can reduce maintenance time and downtime, while also benefiting from at least a 15% reduction in associated maintenance costs.
e. Minimized Dust Generation and Emission: Low carbon steel shot undergoes gradual size reduction layer by layer during usage, leading to significantly reduced dust generation during shot blasting operations. This reduction in dust translates to a decrease in dust emission of at least 20%, promoting a cleaner and healthier work environment.
Property | Value |
---|---|
Chemical Composition | C 0.06-0.12% Si 0.12-0.3% Mn0.25-0.5% S 0.045% P 0.05% |
Size | 0.2mm-3.0mm |
Name | Grinding Pills |
Features | Strong Impact Resistance Stable Performance |
Production Process | Refined By Drawing, Cutting, Strengthening And Other Processes |
Hardness Deviation | -3.0-3.0HRC |
Application | Springs, Connecting Rods, Crankshafts, Gears, Rocker Arms, Camshafts And Other Components Subject To Alternating Torque In The Automotive Industry, As Well As Other Industrial Fields |
Hardness | HRC 36-52 |
Mild Steel Shot | Yes |
Stainless Steel Pills | Yes |
Metal Processing Excellence: Grinding pellets are widely utilized in the metal processing industry to achieve a smoother and more uniform metal surface by removing oxide layers, scratches, welding slag, and other surface imperfections. They are versatile and can be employed for grinding and polishing various metal products, including castings, forgings, steel, aluminum, stainless steel, and more.
Automotive Precision: The automotive industry extensively relies on grinding pellets for manufacturing and repair purposes. These pellets are commonly employed in the surface treatment of automotive parts, including engine components, body parts, wheels, and more. Their usage enhances the surface quality and smoothness of these parts, ultimately improving their overall performance and visual appearance.
Aerospace Excellence: Grinding pellets play a crucial role in the aerospace industry, specifically for grinding and polishing aerospace engine parts, aircraft structural components, and more. Their application is vital in ensuring that the surface quality of these critical parts meets the demanding standards set by the aerospace industry.
Electronics Industry Precision: Grinding pellets find wide application in the electronics industry for the surface treatment of electronic components and semiconductor devices. By removing welding slag, oxide layers, and other contaminants, grinding pellets significantly improve the surface finish and electrical performance of these components. This is vital in ensuring the reliability and functionality of electronic devices.
Precision Machining Expertise: Grinding pellets are widely embraced in the field of precision machining, catering to the grinding and polishing needs of optical components, watches, jewelry, and other precision parts. Their usage enables the attainment of high-precision and high-finish surfaces, meeting the stringent requirements of precision machining processes.
Inner packaging: 25kg/bag with inner film bag.
Outer packaging: nylon woven bag, kraft paper bag, carton.
Whole ton packaging: pallet or ton bag.